Технология подготовки углеотходов к использованию в дорожном строительстве
Для получения материала, пригодного для основания, предлагается следующая технология. Горелая порода терриконов дробится, в результате чего слабопрочная плохообоженная составляющая разрушается и после грохочения в составе фракции менее 2 мм удаляется в отвал. Оставшаяся крупнообломочная фракция подвергается второму этапу дробления до выхода 30-40% мелкозема. Затем полученная смесь активизируется добавками 3-10% извести или цемента. В качестве активатора можно применять граншлак, некоторые другие виды неорганических вяжущих. Полученный из такой смеси после увлажнения и уплотнения слой в расчетный период обладает достаточно высоким модулем упругости – 300-600 МПа, что позволяет применять его в конструкциях дорожных одежд любых технических категории.
1 – конструкция дорожной одежды; 2 – укрепленная обочина; 3 – защитный слой из глинистых грунтов; 4 – пожаробезопасная прослойка; 5 – углеотходы; 6 – защитный слой из дробленых углеотходов.
Рисунок – Конструкция насыпи из углеотходов
Технология брикетирования
Транспортирование брикетов в сушильную камеру
С технической стороны для выполнения условий брикетирования без использования связующих добавок в наиболее полной мере подходят шнековые экструдеры, успешно применяемые для формования высокопластичных строительных материалов и пластмасс. используя этот принцип, специалисты ИОТТ, ООО «Брик-Тек» и ООО «ИТ «Северная Русь» при содействии АО «ННЦ ГП-ИГД им. А.А. Скочинского» разработано специализированное прессовое оборудование для производства механически прочного брикетного топлива из угольных шламов без связующих добавок. Для формирования брикетов в составе технологического комплекса используется специализированное шнековое оборудование.
Разработанная технология позволяет в максимальной мере реализовать теоретические принципы брикетирования без связующих присадок за счёт создания, при окусковании шламов, в зоне прессования, комбинированного действия осевых, сдвигающих и крутящих усилий при уплотнении частиц брикетируемого под давлением материала.
По состоянию на 01.08.2016 г. в г. Воркуте при поддержке Правительства республики коми и привлечении средств инвесторов смонтирована и начала действовать модульная опытно-промышленная брикетная линия, на которой отрабатываются все технологические режимы от приготовления смеси и дозирования сырьевых компонентов, формирования и сушки брикетов, пакетирования и отгрузки готовой продукции.
Угольные брикеты обладают прочностью, необходимой для их последующей транспортировки. Сохраняют прочность при увлажнении, обладают однородностью по геометрическим и физико-химическим параметрам. Проектная производительность брикетной линии составляет Q = 5,0 Т/ч.
Залежи угля
Ведущая отрасль промышленности — угольная. Это сырье относится к старейшим видам топлива. До самого 19 века в России помещения отапливали дровами, древесина использовалась для работы транспорта и механизмов.
Первые месторождения угля, которые были обнаружены:
- Донецкий бассейн;
- Сибирь;
- Восток.
Новый вид топлива использовался для поездок на транспорте, отопления жилых домов и производственных помещений, выработки электрической энергии, в химической промышленности и технологической сфере.
Каменное топливо ценится выше, так как у него больше теплота сгорания, а также качество. Сырье можно транспортировать на значительные расстояния. Бурый уголь чаще используют в регионах добычи, так как во время перевозки он раскалывается на мелкие кусочки.
Топливо добывают двумя способами — открытым и шахтным. Последний используется в том случае, если сырье залегает глубоко в земной поверхности. Для этого нужно раскопать шахты. А когда уголь лежит на глубине не более нескольких метров, то разрабатывают карьеры. Такой способ добычи называется открытым. Он более дешевый по сравнению с шахтным.
Методы добычи и разрабатываемые бассейны в таблице:
Шахтный способ | Донецкий |
Печорский | |
Кузнецкий | |
Иркутский | |
Подмосковный | |
Тунгусский | |
Открытый способ | Ленский |
Южно-Якутский | |
Канско-Ачинский | |
Тунгусский | |
Иркутский | |
Кузнецкий | |
Подмосковный |
Последние четыре бассейна разрабатывают смешанным методом. То есть там есть и карьеры, и шахты. Самым большим считается Кузбасс или Кузнецкий. Второе место по значимости для топливной промышленности занимает Канско-Ачинское месторождение.\
Приготовление водоугольного топлива
Актуальность использования водоугольного топлива на ТЭЦ обусловлена появлением новых технологий его приготовления и сжигания, исключающих ранее выявленные недостатки. Суть новой технологии приготовления ВУС состоит в том, что смесь углесодержащих материалов с водой подвергается кавитационному воздействию в специальных аппаратах — кавитационных диспергаторах. Результатом кавитационной обработки, характеризующейся чрезвычайно высоким уровнем местного динамического, компрессионного и температурного воздействия на обрабатываемый материал, является не только измельчение твердого компонента смеси до микронной степени дисперсности, но и появление на поверхности его частиц свойств ярко выраженной гидрофильности.
В отличие от традиционной ВУС кавитационное водоугольное топливо (КаВУТ) стабильно на протяжении длительного времени (контрольные образцы выдерживались в течение 4-х лет) и пластично без каких-либо присадок при достигнутом содержании твердого вещества до 65%.
Технологический процесс приготовления КаВУТ характеризуется низкими удельными показателями энергозатрат (до 30 кВт.ч/т) и расхода металла рабочих органов кавитаторов (менее 100 г на тонну угля), компактностью технологической схемы, простотой в эксплуатации и ремонтном обслуживании.
Удельные затраты на производство КаВУТ составляют 200 руб./т. Удельные затраты на сооружение установки по приготовлению КаВУТ составляют 1,4 млн руб./(т/ч). Удельный объем здания установки приготовления КаВУТ — 40-50 м3/(т/ч).
Технологическая схема и общая компоновка узла приготовления КаВУТ приведена на рис. 1.
Теоретические основы брикетирования
Станислав Будаев
Известные штемпельные, кольцевые и вальные технологии брикетирования углеродосодержащих материалов, с высокой жёсткостью, твёрдостью и упругостью, по принципу действия и особенностям конструкции формовочных инструментов не позволяют, получать механически прочное окускованное топливо без использования связующих веществ с приемлемыми технико-экономическими показателями брикетного производства.
Мировая практика подтверждает: изготовление угольных брикетов без применения связующих добавок по традиционным технологиям требует больших производственных затрат, предусматривающих сверхтонкий помол исходного сырья для прессования, высокотемпературный нагрев брикетируемого материала до пластического состояния и сверхвысокие давления прессования.
Концептуально, с позиций существующих представлений о механизме действия молекулярных и капиллярных сил сцепления при образовании структуры окускованного углеродосодержащего материала с учётом его упруго-пластичных свойств, значительно более благоприятные условия для окускования жёстких, малопластичных веществ без связующих добавок, в сравнении с существующим технологиями прессования, могут быть реализованы только в прессовых агрегатах, обеспечивающих выполнение следующих условий:
— интенсивное развитие активной (удельной) поверхности и капиллярно-пористой структуры брикетируемой массы, а также увеличения числа и плотности контактов брикетируемых частиц в процессе их уплотнения под давлением для повышения эффективности действия молекулярных и капиллярных сил сцепления при формировании структуры окускованного топлива;
— снижение сопротивляемости брикетируемой массы в процессе её уплотнения, обусловленной твердостью частиц и силами трения между ними при их относительном перемещении в межзерновом (межпоровом) пространстве для минимизации энергозатрат на хрупкие деформации, уплотнение и увеличение доли энергии на пластические необратимые деформации, которые определяют механическую прочность структуры брикета;
— повышения активности силового поля поверхности брикетируемых частиц (повышение свободной поверхностной энергии) образования новых некомпенсированных молекулярных и электрических сил взаимодействия за счёт деформации кристаллической решётки и разрушения насыщенного окисленного слоя на поверхности частиц;
— существенное увеличение времени действия давления прессования, что способствует более глубокому сдвигу прилагаемой энергии в сторону образования пластической деформации, которые с механической точки зрения в итоге и определяют прочность образованной структуры окускованного топлива.
Реконструкция котлов
При переводе котлов на сжигание КаВУТ, как правило, в котельном отделении вместо бункеров и питателей угля появляются баки (силосы) для жидкого КаВУТ и компактные трубопроводные системы. Подача и распределение КаВУТ осуществляется с помощью насосов.
Для котлов малой мощности с имеющейся решеткой кипящего слоя реконструкция топочной камеры имеет минимальный объем и заключается в установке форсунок для подачи КаВУТ (рис. 3). КаВУТ подается через прямоточный канал форсунки и разбрызгивается за счет подачи первичного воздуха от дутьевого вентилятора. Сам котел также принципиально не изменяется, дополнительно предусматривается только установка подогревателя вторичного воздуха. Общий вид реконструированного котла на объекте представлен на рис. 4.
Для котлов большой мощности требуется замена нижней части топочной камеры с установкой решетки кипящего слоя и специальных вихревых горелок. Под решетку подводится первичный воздух, над решеткой организуется подача инертного материала в слой и топлива (50-70% от общего расхода на котел), а также возврат несгоревших частиц. Для растопки котла и разогрева слоя инертного материала требуется установка растопочных газовых горелок. Выше, над слоем, устанавливаются основные комбинированные горелки, в которые подаются остальные 30-50% топлива.
В целом при реконструкции котла сохраняется его профиль, каркас, компоновка поверхностей нагрева и прочие основные узлы. Изменения преимущественно касаются схемы газовоздухопроводов, установки системы улова и возврата несгоревших частиц и реконструкции топочной камеры.
Переработка отходы ископаемое
Горное производство, как и любое другое не бывает безотходным, однако до середины ХХ века горнодобывающая промышленность не рассматривала образующиеся отходы как серьезную проблему. Темпы добычи и переработки полезных ископаемых увеличивались вместе с количеством образующихся отходов на предприятиях. Причем в последнее время показатель роста объемов производственных отходов стал существенно превышать выход выпускаемой продукции. Руды стали беднее (падает содержание извлекаемого ценного компонента), условия разработки месторождений усложнились, а образующиеся отходы в виде вскрышных, отвальных и пустых пород, а также хвостов технологического цикла неизбежно возрастают. По статистике под породные отвалы выделяется 0,1 Га земельной площади. В реальности же отвалы занимают площади гораздо обширнее, около 100 млн. гектар, причем земля, находящаяся под этими отвалами может быть вполне плодородной. Рекреационная способность природы уже не справляется с возрастающим количеством образующихся отходов, что приводит к необратимым последствиям загрязнения окружающей среды.
С другой стороны, отходы горнорудной промышленности при этом имеют некоторый ресурсный потенциал, отвалы служат источником дополнительного производства, из некогда заброшенных забалансовых и беднобалансовых отвалов активно извлекается уран, золото, редкие и редкоземельные металлы. Наряду с этим отходы горных производств используются в качестве строительных материалов, а также для закладки выработанного пространства шахт и карьеров.
Переработка отходов горных производств, как правило, связана с потребностями смежных отраслей в сырье. Технологические исследования по утилизации показали возможность комплексной переработки многих полезных ископаемых с полным или частичным переходом на производство различных видов продукции из образующихся отходов.
Складирование отходов горнодобывающей отрасли требует анализа и сопоставления экономических затрат и возможных доходов от их утилизации. Следует учитывать, что хранение отходов в качестве минерально-сырьевых источников для последующей переработки несет в себе определенные затраты на их содержание (тарифы за поверхностное хранение, организация защитных мероприятий от вымывания, окисления, выветривания и т.п.). Переработка накопившихся горнорудных отходов способствует экономии минерального сырья, позволяет высвобождать огромные площади плодородных земель, значительно снижает негативные последствия загрязнения окружающей среды, сокращает затраты на геологоразведочные мероприятия и разработку новых минеральных и сырьевых месторождений.
Конечно, было бы гораздо эффективнее, если разработать такие производственные и технологические процессы, при которых отходов не было бы совсем, но, к сожалению, для горнодобывающей отрасли, впрочем, как и для многих других, это практически трудноразрешимая задача.
Учет пожароопасных свойст углеотходов
При конструировании насыпи из углеотходов важное место отводится мероприятиям, предупреждающим высокотемпературный саморазогрев. Расчеты пожаробезопасных элементов показали, что самовозгорание углеотходов зависит от их зольности, марки добываемого или обогащаемого угля, энергии активации и некоторых других параметров
Для земляного полотна автомобильных дорог установлена критическая величина отсыпаемого слоя в 5, 2 – 12 м. При превышении этих размеров в теле насыпи из углеотходов предусматривается устройство пожаробезопасных прослоек из связного грунта толщиной не менее 0, 15 – 0, 40 м (рис. 1), либо другим материалом, препятствующим поступлению атмосферного кислорода в структуру углеотходов.
Особенности технологий строительства насыпей из углеотходов в основном связаны с необходимостью ликвидации потенциальной просадочности и создания плотной бездеформативной структуры с заданным содержанием мелкозема. Сложные инженерно-геологические условия, возможность подтопления и даже затопления земляного полотна требуют создания максимально плотной структуры по всему объему насыпи.
Применения углеотходов дорожниками Донбасса позволило получить значительный экономический эффект. Кроме того, в отрасли сокращаются затраты на содержание отвалов; в сельском хозяйстве уменьшаются потери плодородных земель, изымаемых под складирование отвалов. Значителен также природоохранный эффект, что способствует улучшению экологической обстановки Донбасса.
Н.С.Коршунова, М.М.Перистый
Донецкий национальный технический университет
Охрана окружающей среды и рациональное использование природных ресурсов — 2011
Материалы ХXI Всеукраинской научной конференции аспирантов и студентов
Список литературы
- УкрНИИ Углеобогащение. Отчет по теме “Исследование свойств отходов обогащения углей и породных отвалов в Донецком и Львовско-Волынском угольных бассейнах”. Луганск, 1984.
- Цыганков В.Н., Михович А.С. Отвальная порода углеобогащения как строительный материал для плотин, дамб // Сборник научных трудов. — 2005. — № 3— C.762-765.
- Зборщик М.П., Осокин В.В. Предотвращение самовозгорания горных пород.—К.: Техника, 1990.—176с.
Нефтяной кокс в качестве топлива
Не так давно появился еще один очень перспективный вид отходов — нефтяной кокс, являющийся твердым остатком глубокой вторичной переработки тяжелых нефтепродуктов. Значительные объемы получения такого отхода в ближайшей перспективе при особенностях этого продукта отразятся на топливном балансе и оборудовании энергетики.
При малой зольности (<1%) и высокой теплотворной способности (до 8000 ккал/кг) нефтекокс, тем не менее, не относится к высокосортному топливу из-за высокого содержания серы (4-7%) и ванадия (до 0,15%). К тому же, незначительный выход летучих (8-12%) определяет низкие реакционные свойства нефтекокса, что, при высоких коррозионных и шлакующих свойствах, требует специальных методов и устройств для использования его в энергетике. На текущий момент в мире наиболее распространены способы сжигания нефтекокса в котлах, оборудованных топками с циркулирующим кипящим слоем с вводом в топку сорбента для связывания серы. Также нефтекокс сжигают в смеси с углем в пылеугольных котлах, оснащенных эффективными системами сероочистки и азотоподавления. Затраты на такой комплекс очистки составят не менее 30% от общей стоимости строительства объекта. При этом оптимальных решений проблем шлакования не найдено.
Набор проблем, связанных с использованием нефтекокса в энергетике, по ряду показателей сопоставим с проблемами сжигания в энергетических котлах антрацитов и отходов их обогащения. В основе предлагаемой нами технологии сжигания нефтекокса лежит идея получения из него, с использованием кавитационных устройств, водной суспензии и сжигания такого КаВУТ в низкотемпературном кипящем слое инертного материала.
Высокое содержание серы в нефтекоксе может отрицательно сказаться на эффективности использования известных схем мокрых и мокросухих способов связывания оксидов серы, оставляя без защиты от сернокислой коррозии хвостовые участки котла (воздухоподогреватели, золоуловители и газоходы). Необходимо также принимать в расчет наличие в составе нефтекокса значительного количества ванадия и обязательной необходимости связывания его оксидов уже на начальных участках топки котла для исключения высокотемпературной ванадиевой коррозии ширмово-конвективных поверхностей нагрева. Для проверки влияния этих особенностей нефтекокса на процесс кавитационной переработки его в КаВУТ и на процесс сжигания полученного топлива проведены стендовые огневые испытания, основные результаты представлены в табл. 2. При этом опробовано приготовление и сжигание различных вариантов КаВУТ из нефтекокса.
Проведенные испытания подтвердили технологическую работоспособность и экологическую эффективность двухступенчатого сжигания КаВУТ из нефтекокса.
По результатам экспериментальных и расчетных исследований разработаны схемы сжигания и конструкции топочно-горелочных устройств для котлов большой и малой мощности.
Гидротранспортирование угля состояние проблемы
Гидравлическое транспортирование твердых сыпучих материалов получило развитие во второй половине ХХ века. В настоящее время получил распространение трубопроводный транспорт нефти, природного газа и нефтепродуктов. При помощи магистральных гидротранспортных систем осуществляется перемещение полезных ископаемых и строительных материалов, промышленных отходов и химического сырья.
Существует две принципиально разные технологии гидравлического транспортирования угля.
Первая технология – транспортировка в гидросмеси массовой концентрацией С = 50% с последующим обезвоживанием на приемном терминале. Уголь дробят до крупности 0-1 (3-6) мм и смешивают с водой (соотношение жидкости и твердого составляет 1: 1).
Один из первых в мире – магистральный углепровод шахты Блэк-Меса (Аризона, США), длиной 439 км и производительностью 5,8 млн. т / год. В 1964 г. энергетическая компания Peabody Energy подписала контракт с племенами навахо и ТАПИ об использовании их водных ресурсов для создания гидросмеси и ее дальнейшей транспортировки на ТЭС в Мохейви, мощностью 790 МВт.
Процесс требовал большого количества воды, что вызвало экологический кризис на этих территориях. Под натиском социальных и этно-религиозных движений углепровод несмотря на технологическую пригодность и экономическую эффективность был законсервирован 31 декабря 2005. p>
На обезвоживающей фабрике углепровода Блэк Меса вся масса пульпы подогревалась до 70 ° C, затем обезвоживалась в центрифугах с диаметром ротора 1000 мм и скоростью вращения 1000 мин. Кек влажностью 20% подвергался термической сушке в мельницах-сушилках. Нагрев пульпы перед центрифугированием снижал влажность кека с 28 до 20%. Фугат, в который шло 6,5% угля, или сжигался в виде ВВВС, или складировали в илонакопитель. Вследствии сложности получения ВВВС в первые годы работы углепровода, в илонакопители собралось большое количество твердой фазы фугата, что представляло опасность для окружающей среды. P>
Вторая технология гидравлического транспортирования угля – в виде высококонцентрированных водо-угольных суспензий (ВВВС). [] На приемном терминале ВВВС используют как водо-угольное топлива (ВУТ). P>
Классический способ приготовления ВВВС состоит из трёх основных стадий(рис.1.4):
- Дробление рядового угля до крупности 10 .. 20мм;
- Мокрое измельчение угля (в присутствии воды и пластификатора) до 0.1-0.2 мм;
-
Гомогенизация, хранение, транспортирование.
Рис. 1.4 – Схема приготовления ВУТ
Для помола используют шаровые или стержневые барабанные мельницы со специальным набором помольных тел, что обеспечивает нужный бинарный гранулометрический состав угольной фазы. Этот этап является ключевым при приготовлении ВУТ, поскольку определяет дальнейшие характеристики ВУТ (гранулометрический состав, вязкость, стабильность и т.д.). Кроме того, данный этап обычно является наиболее энергозатратным.
На стадии мокрого помола в состав ВУТ могут быть включены различные добавки, необходимые для увеличения статической стабильности ВУТ, снижение вязкости и другие.
Золотосодержащие продукты переработки нерудного сырья и отходы горно-химического производства и топливно-энергетического комплекса
- содержание золота в исходных ПГС изменяется от первых миллиграмм до 60 мг/м3;
- в отложениях ПГС преобладает тонкий металл (класс менее 0,15 мм) пластинчатых и уплощенных форм с очень низким весом отдельных золотин;
- ПГС Сымского месторождения содержат кроме золота платиновые металлы.
1.2.3.Наш опыт работ по включению аппаратов гравитационного обогащения (шлюзов мелкого наполнения) в технологическую схему при «мокрой» переработке ПГС на дробильно-сортировочных фабриках (ДСФ), полученный на Песчанской ДСФ и землечерпательном снаряде ПЧС-609, показал сложность решаемой задачи. При полупромышленных испытаниях устройств шлюзового типа уровень извлечения металла не превысил 6 %. Низкое извлечение золота обусловлено малой гидравлической крупностью подавляющей части золотин, а также трудностью ввода золотоизвлекающего устройства в оптимальный режим работы без ущерба для основной технологии обогащения песков. Представляется, что и более совершенные аппараты гравитационного обогащения, способные извлекать тонкое и мелкое золото (концентратор Knelson, Итомак и др.), не смогут обеспечить рентабельного извлечения металла из ПГС из-за его низкого содержания (первые десятки миллиграммов) и больших объемов перерабатываемой смеси (Михнев, Рюмин, 1998; Полькин, 1987). Проблема может быть решена с использованием высокопроизводительных предконцентраторов, т.е. устройств, позволяющих концентрировать большую часть золота в малом объеме промежуточного продукта и непрерывно выводить его из основной технологической цепи для переработки на более эффективных аппаратах. Роль предконцентраторов, вероятно, могли бы выполнять отсадочные машины, винтовые сепараторы и гидроциклоны. К сожалению, все это значительно усложняет технологическую схему переработки песков и может свести к минимуму рентабельность работ по попутному извлечению золота из ПГС.Предварительная концентрация золота при добыче и переработке золотоносных ПГС может быть осуществлена и без применения специальных устройств. Такой процесс отмечен при добыче ПГС земснарядами и складировании их на картах намыва на месторождениях Ачинского речного порта (р. Чулым), Урюпском месторождении, а также изученном нами Защитнинском месторождении на р. Иртыш, разрабатываемом Усть-Каменогорским комбинатом нерудных материалов. Во всех случаях головные части карты намыва, где происходит излияние пульпы, многократно, а иногда и в десятки раз больше относительно исходного содержания, обогащались золотом. Карта намыва при этом работает как естественный шлюз. Такой механизм обогащения объясняется теоретическими посылками и экспериментальными работами и неоднократно отмечался нами на эфельных отвалах россыпных месторождений, складируемых самотеком (Макаров, 1997). Поскольку процесс формирования карт намыва управляем, для золотоносных ПГС возможно направленное обогащение головных частей и их последующая селективная переработка на предмет извлечения золота.
Применение каменного угля в современном мире
Различно применение полезных ископаемых. Каменный уголь изначально был только источником тепла, потом энергии (превращал воду в пар) теперь же в этом плане возможности угля просто неограниченны.
Тепловую энергию от сжигания угля преобразовывают в электрическую, из него изготавливают коксохимическую продукцию и извлекают жидкое топливо. Каменный уголь — единственная порода, в которой в виде примесей содержатся такие редкие металлы, как германий и галлий. Из него добывают перерабатываемый потом в бензол, из которого выделяют кумароновую смолу, идущую на изготовление всевозможных красок, лаков, линолеума и резины. Из каменного угля получают фенолы и пиридиновые основания. При переработке находит каменный уголь применение в производстве ванадия, графитов, серы, молибдена, цинка, свинца и еще множества ценных и незаменимых сейчас продуктов.
Уголь важен для народного хозяйства
Каменный уголь — это один из первых минералов, который человек начал использовать в качестве топлива. Только в конце 19 века его стали постепенно вытеснять другие виды топлива: сначала нефть, потом продукты из нее, позднее газ (природный и полученный из угля и других веществ). Каменный уголь применяется в народном хозяйстве очень широко. Прежде всего, как топливо и химическое сырье. Например, металлургическая отрасль промышленности при выплавке чугуна не может обойтись без кокса. Производят его на коксохимических предприятиях из каменного угля.
Где еще используют уголь?
На отходах добычи каменного угля (антрацитовом штыбе) работают мощные тепловые электростанции в России и Украине (и не только). Впервые получили металл с использованием кокса из железной руды в 18 веке в Англии. Это в металлургии стало началом применения каменного угля, точнее, кокса — продукта его переработки. До этого железо получали при помощи древесного угля, поэтому в Англии в 18 — 19 веках вырубили почти весь лес. Коксохимическая промышленность использует каменный уголь, перерабатывая его в каменноугольный кокс и коксовый газ, при этом выпускаются десятки видов химических продуктов (этилен, толуол, ксилолы, бензол, коксовый бензин, смолы, масла и многое другое). На основе этих химических продуктов изготавливают самые разные пластмассы, азотные и аммиачно-фосфорные удобрения, водные растворы аммиака (удобрения), химикаты для защиты растений. Также производят моющие средства и стиральные порошки, лекарства для людей и животных, сольвенты (растворители), серу или серную кислоту, кумароновые смолы (для красок, лаков, линолеума и для резинотехнических изделий) и т. д. Полный перечень продуктов коксохимической переработки каменного угля занимает несколько страниц.
Как складывается стоимость угля?
Кокосовый уголь — что это?
Один из видов древесного угля — кокосовый уголь, который изготавливают из скорлупы орехов. Его можно применять в мангалах, грилях, барбекю. Он горит гораздо дольше другого древесного угля, не имеет запаха, в нем нет серы, он не воспламеняется от капающего жира. Очищенный кокосовый уголь может использоваться для кальяна, т. к. при использовании не имеет ни запаха, ни вкуса. После специальной обработки (активирования) рабочая поверхность каждого кусочка угля увеличивается в несколько раз (и он становится прекрасным адсорбентом). Использование кокосового угля в фильтрах для очистки воды дает прекрасные результаты.
Обзор установок брикетирования отходов от «ЖАСКО»
Многие предприятия уже убедились в целесообразности использования таких агрегатов. Клиенты решили проблему с отрицательной стоимостью отходов, вышли на полное самоотопление и даже получили прибыль благодаря установке.
Так, к примеру, один из наших постоянных партнеров – крупозавод, перерабатывает в среднем до 40 т гречихи в сутки. В результате на производстве остается огромное количество отходов, которые до приобретения установки брикетирования утилизировались на свалках. На это тратились немалые средства: транспорт, утилизация в соответствии с нормативной документацией и т.д. После приобретения установки брикетирования расходы на переработку не требуются, кроме того – она приносит выгоду.
Наш партнер поделился результатами использования машины: «Установку брикетирования обслуживает 1 человек в смену, работа идет круглосуточно, а профилактические работы производятся всего раз в неделю. Основная масса полученных брикетов идет на топку собственных котельных на крупозаводе, а 30-40% продается».
Самым привлекательным для предприятий в установке является то, что она способна переработать сырье, которое изначально имеет отрицательную стоимость. Иными словами, агрегат позволяет получить выгоду там, где обычно производство терпит убытки – вместо затрат на хранение и утилизацию отходов, вы можете получить прибыль за счет производства высококачественного топливного брикета.
Сами брикеты – выгодный вид топлива. Давайте разберемся, чем же он выгоден по порядку и начнем с цифр. Например, количество остатков при сгорании опилочного брикета не превышает одного процента, когда зольность обычного топлива (того же угля), может достигать 40%. И, кстати, даже этот 1%, который таки оставляют брикеты можно использовать и дальше – уже в виде калийного удобрения.
Теплотворная способность брикетов тоже занимает лидирующие позиции: она опережает древесину в 1,5 раза и составляет 4,5-5 кВт/кг. Это значит, что брикета весом в килограмм достаточно для обогрева дома площадью 50 квадратных метров в течение часа. Так, например, если сжечь 1000 кг топливных брикетов, то выделится столько же тепла, сколько дает 1600 кг древесины, 478 куб. м газа, 500л дизельного топлива или 1000 кг угля.
Кроме перечисленного, топливные брикеты из растительных отходов – экологически чистый продукт, при сжигании которого оказывается минимальное негативное воздействие на окружающую среду.
А также брикеты удобны в хранении – они уплотнены в 4-12 раз и занимают гораздо меньше места, чем изначальное сырье. Низкая себестоимость, возможность использования в котлах любой мощности, длительное горение – продолжать список преимуществ брикетированного топлива можно бесконечно долго.
Суть работы самой установки заключается в прессовании сырья при высокой температуре. Связующим элементом в процессе переработки выступают вещества, содержащиеся в клетках растений. Они плотно «склеивают» сырье. На поверхности брикетов при переработке образуется науглероженной слой, который делает готовый продукт более прочным.
УБО может работать как автономно, так и в составе линии. На рынке представлено не много похожей техники, но даже среди существующих аппараты от «ЖАСКО» отличаются высокой производительностью, надежностью, простотой эксплуатации и универсальностью.
Брикетирование растительных отходов – это не просто переработка отходов, но путь к повышению безотходности производства, избеганию трат на утилизацию и получению дополнительных доходов.
Акция месяца! При покупке установки брикетирования отходов УБО-3 до 31 октября — 100 тысяч рублей в подарок.
Безотходное производство: обработка шлака и золы
После сжигания отходы уменьшаются на 90% в объеме. После термической переработки мусора остаются зола и шлак.
Шлак – это пятый класс опасности отходов, такой же класс опасности имеют несортированные отходы. Он может сразу применяться для отсыпки дорог. Предварительно из шлака отбираются черные и цветные металлы, которые впоследствии направляются на переработку.
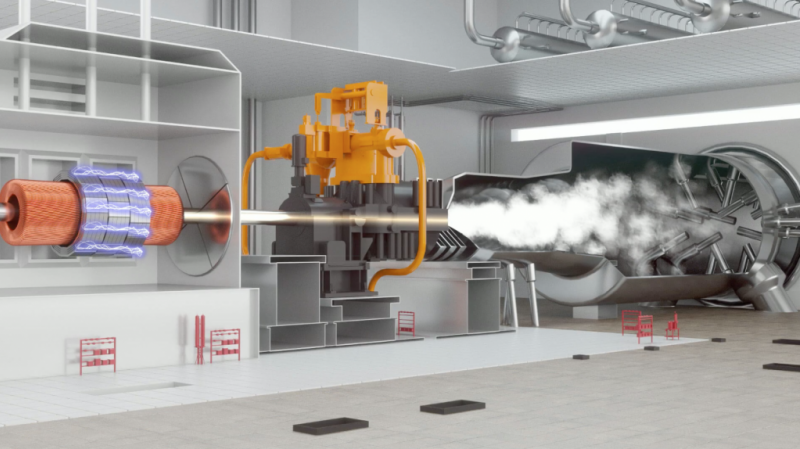
Проект «Энергия из отходов»
Летучая зола составляет примерно 3-5% от перерабатываемых отходов и относится к более высокому, третьему, классу опасности. Поэтому «РТ-Инвест» планирует строительство в Московской области также завода для переработки такой золы в строительный материал по технологии Carbon8. Эта технология получила признание ООН и была удостоена награды за вклад в циклическую экономику Евросоюза.
Carbon8 представляет собой химическое обезвреживание золы методом ускоренной карбонизации. Из третьего класса опасности зола обезвреживается до сырья для производства строительных материалов. Зола успешно превращается в различные блоки, бордюры, плитку и даже может заменить цемент. Таким образом, новые технологии предоставляют уникальную возможность – не зарывать под землю ни одного килограмма мусора.
Выводы
Одним из направлений технического прогресса является развитие трубопроводного транспорта. Наибольшие перспективы имеет промышленный и магистральный гидротранспорт нефти и сыпучих материалов. Гидротранспорт характеризуется непрерывностью и равномерностью грузопотока, повышенной надежностью, возможностью полной автоматизации, независимостью от погодных условий, имеет экономическое преимущество над железнодорожным транспортом, особенно, когда шахты находятся в отдаленных районах; создает меньше шума, имеет существенно меньшие транспортные потери и техногенную нагрузку на окружающую среду; малые сроки строительства.
Существует несколько способов гидравлического транспортирования угля:
- пульпопроводом с дальнейшим обезвоживанием;
- транспортирование высококонцентрированного водугольного топлива.
Отрицательные свойства бурого угля, препятствуют использованию гидротранспорта, для решения этой проблемы предложена технология обработки угля аполярнимы реагентами – масляная агрегация. P>
Под масляной агрегацией угля понимают совокупность процессов структурирования тонкой полидисперсной угольной фазы (размер зерен до 3-5 мм) в водной среде с помощью масляных реагентов. В основе этих процессов лежит механизм адгезионного взаимодействия олеофильной угольной поверхности с маслами, в результате которого достигается ее селективное смачивание и агрегатирование в турбулентном потоке воды. Гидрофильные частицы не смачиваются маслом и не входят в состав агрегатов, что позволяет выделять их в виде породной суспензии. P>
Исходя из изложенного для облагораживания бурого угля при его гидротранспортировании, нами выбрана технология масляной агрегации угля, которая хорошо сочетается с технологиями его дальнейшей переработки и использования: брикетирование, ожижение, газификация, пиролиз. P>